Aerocat:
Full polymer catering trolley
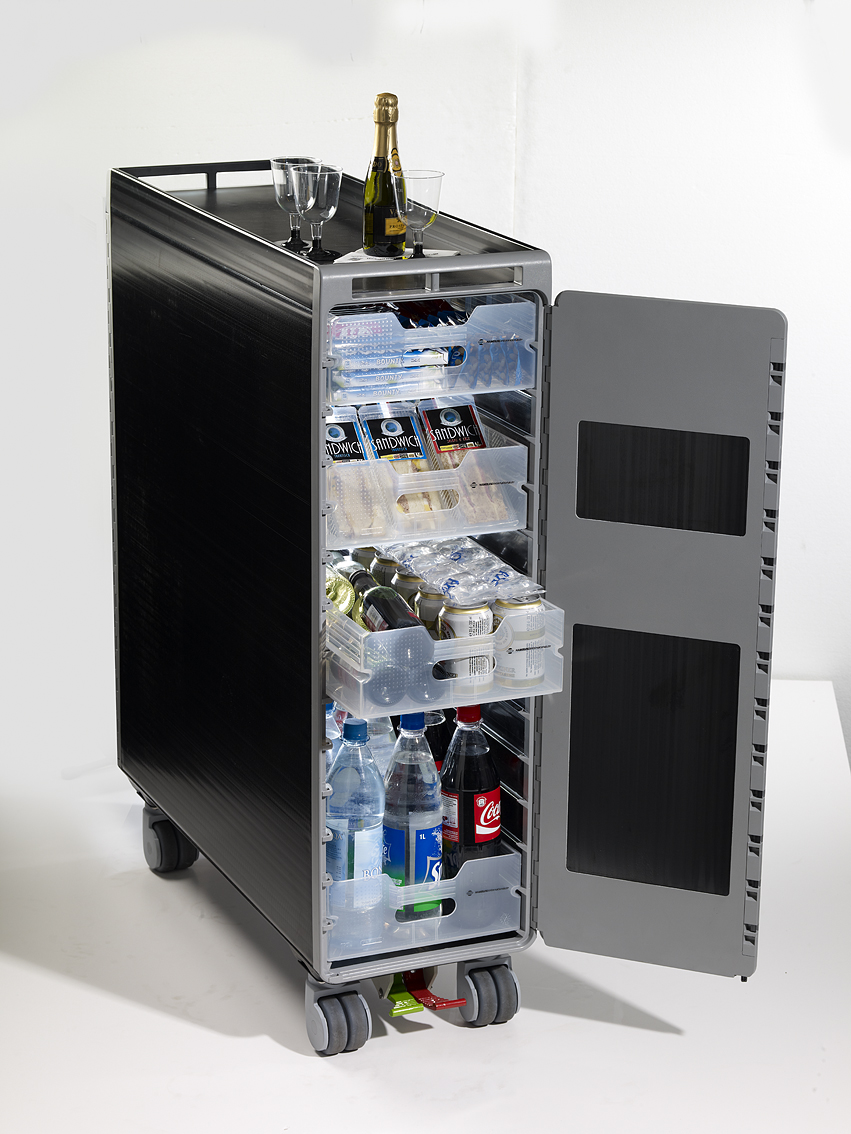
Together with the AeroCat alliance – Promolding innovated the aluminum airline catering trolley into an EASA and ETSO certified full polymer trolley. The TIGRIS trolley distinct from any other competitive product in the market. The TIGRIS trolley provides a substantial contribution to a greener, healthier and safer airline environment as a whole and airline catering logistics more in specific. A casters alignment system is an available option.
Passengers or operator benefits:
General benefits
The TIGRIS trolley will enable changing the airline catering logistics substantially. The trolley introduces new polymer applications to the industry, thus being able to optimize existing catering operations and shaping the industry for future innovative solutions. More specific, airlines will realize a high return on their investment by substantial fuel reductions, less maintenance costs, an attractive residual value of their investment, lower spendings on chilling food and beverages on board, longer lifetime and the possibility for future trading of emission rights (2012, ETS law), due to the low carbon footprint. Furthermore substantial savings can be realized by the related effect – using RFID technology – on the overall catering logistics. Additional value will be realized by attendant’s increased satisfaction on the several improved ergonomic aspects of the trolley and its aesthetics. Overall the airline has an attractive opportunity to contribute to a better world and thus creating an improved environmental friendly image for the airline industry.
Reducing negative effects in the environment
The trolley is from the design phase eco-designed for closed loop recycling, with the lowest carbon footprint in its kind (reference: Life Cycle Assessment of TNO).
Compared to aluminum trolleys, TIGRIS trolleys reduce the carbon footprint by a factor 2.2, not taking into consideration the differences in the use phase as a result of lower weight. The main difference comes from the differences in material production and the CO2 bonus for the end-of-life recycling of the trolley.
If saved CO2 emissions could be traded.
REDUCING THE TOTAL COST OF OWNERSHIP OF OPERATORS
The TIGRIS trolley will lower the Total Cost of Ownership substantially.
In most scenarios the IRR calculation shows attractive returns with already 100% ROI in the first year.
THE SPECIFIC BENEFITS OF THE TIGRIS TROLLEY
Security
Fully sealed and will prevent putting unwanted items between the walls of the trolley, thus improving the overall safety on board;
Life extension
The predicted lifetime is at least 10 years, by normal wear & tear;
Maintenance
The trolley body is developed with a ‘No Maintenance’ philosophy in mind;
Aesthetics
A modern and appealing look, that will]contribute to overall passenger satisfaction;
Hygienic
No hidden corners and edges,]therefore easier to clean.
Insulation
Better insulation than aluminum, due to its full polymer body with static air chambers. This will cause less use of dry ice, thus contributing positively to a lower carbon footprint;
Impact resistance
High impact resistance. This will cause less damage to the trolley during the catering process and a longer attractive look;
Ergonomics
Several ergonomic improvements. With these aspects, the airline improves automatically its health- and safety care for personnel, resulting in an overall improved satisfaction of the crew;
Scratch resistance
Visibility of scratches will be minimal by through and through colored polymer, thus maintaining a good look & feel. The overall image of the airline will be better sustained;
RFID enabled
Standard equipped with 4 modern passive RFID tags, approved for airline use, resulting in optimized logistics processes.
THE TECHNOLOGICAL BREAKTHROUGH
A breakthrough design was needed. The objective was to develop a full polymer eco-designed trolley at low cost. The TIGRIS solution is a patented construction that facilitates a low cost- high volume production process in such a way that only virgin polymer material is used, providing a closed loop same level re-use. Furthermore, the full polymer characteristic provides the best situa- tion possible for use of RFID tags.
To develop an environmental friendly trolley, Promolding has chosen to produce its trolley from material that could be closed loop re-used, that would fit mechanical properties, that would be tough enough for misuse and that could face harsh chemical situations (washing street). The choice was made for the PPSU polymer (RADEL R) of Solvay.
The trolley body, a part of the door and the top tray are produced by extrusion. The production is on ‘infinite’ length and subsequently sawed to size. The extrusion made body is of such a dimension and difficulty that it’s unique within the polymer manufacturing industry.
The door is made in a combination of injection molding parts and an ‘inner wall’ extrusion part. Promolding succeeded in developing a door of full polymer by using its unique and patented design on the closing mechanism along the long side of the door panel. Along both long sides of the door, the hinge and the patented door locking mechanism keep the door in place at requested loads for certification
The TIGRIS trolley is developed for fast, high volume, robotized manufacturing thus keeping production costs at attractive levels and preventing low cost labor.